What Is Inventory? Definition, Types, & Examples
- mark599704
- Nov 22, 2023
- 7 min read
Updated: Dec 31, 2024
Inventory refers to a company's goods and products that are ready to sell, along with the raw materials that are used to produce them.
Inventory, also known as stock, is a crucial aspect of any business operation. Inventory can include raw materials, work-in-progress items, and finished goods. In this article, we will define inventory and explore its various types. We will also give examples for each type and discuss why inventory control and management are important.
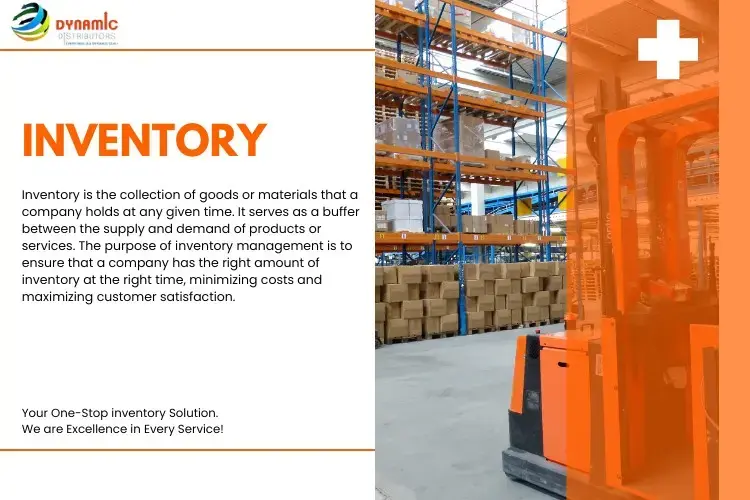
Related Blogs:
What is Inventory?
Inventory is the collection of goods or materials that a company holds at any given time. It serves as a buffer between the supply and demand of products or services. By maintaining inventory, businesses can meet customer demands promptly and maintain a smooth production process. Inventory can be classified into various types, each with its unique characteristics.
Key Takeaways of Inventory
Asset Classification: Inventory is a current asset on a company's balance sheet. It includes the raw materials used in production and the finished goods available for sale.
Valuation Methods: Inventory is valued using different methods, such as first-in, first-out (FIFO), last-in, first-out (LIFO), and weighted average. These methods impact how the cost of goods is accounted for in financial records.
Cost Management: Efficient inventory management helps businesses control costs. It ensures that goods are produced or acquired only as needed, which prevents excess inventory and avoids higher holding costs.
Operational Flexibility: Inventory management allows businesses to adjust production or purchasing based on demand. This helps balance supply with customer needs.
Inventory Valuation Methods
Inventory can be valued in three ways. Here are inventory valuation methods:
First-In, First-Out Method (FIFO): In FIFO, inventory valuation follows the principle of using the oldest items first. Items added to the inventory earliest are presumed to be the first ones sold or utilized in the production process.
Last-In, First-Out Method (LIFO): LIFO means that the newest items added to the inventory are the first to be sold or used. This is the opposite of FIFO.
Weighted Average Method: The weighted average method calculates the average cost of all inventory units. It combines the cost of new items with the cost of existing inventory to give a blended cost per unit.
Types of Inventory
The types of inventory are the following:

Raw Materials: These are the basic materials used in manufacturing processes. They include metals, plastics, fabrics, and chemicals, among others.
Work-in-Progress: Work-in-progress inventory consists of partially completed products that are still undergoing manufacturing processes.
Finished Goods: These are the final products that are ready for sale or distribution to the end customer.
Maintenance, Repair, and Operations (MRO) Inventory: MRO inventory consists of items required to maintain and repair equipment, machinery, and facilities.
Transit Inventory: Transit inventory refers to goods that are moving between different locations. This includes items traveling between warehouses or distribution centers.
Cycle Inventory: Cycle inventory represents the stock of goods that varies with the regular replenishment cycles of a company.
Anticipation Inventory: This type of inventory is held in anticipation of future demand. It is often used for seasonal or promotional purposes.
Safety Stock: Safety stock is extra inventory kept to avoid running out of stock. It helps manage unexpected changes in demand or supply.
Buffer Inventory: Buffer inventory is maintained to protect against uncertainties in demand, supply, or lead times.
Obsolete Inventory: Obsolete inventory refers to items that are no longer in demand or have become outdated. It is important to dispose of obsolete inventory to free up storage space and avoid losses.
Consignment Inventory: Consignment inventory is held by a retailer but is owned by the supplier. The supplier retains ownership until the goods are sold.
Excess Inventory: A retail store ordered more units of a seasonal product than customers wanted. This resulted in unsold items left over after the season.
Decoupling inventory: Decoupling inventory is stock placed in the production process. It helps buffer against disruptions and ensures a smooth workflow.
Theoretical inventory: Theoretical inventory represents an idealized stock level, calculated to meet demand without overstocking or causing delays.
Example Of Types Of Inventory
To better understand the different types of inventory, let's consider some examples:
Raw Materials: A furniture manufacturer holds various types of wood, fabric, and screws as raw materials.
Work-in-Progress: An automobile manufacturer has partially assembled cars on the production line.
Finished Goods: A clothing retailer has a stock of finished garments ready for sale.
MRO Inventory: A maintenance department holds spare parts, tools, and lubricants for equipment maintenance.
Transit Inventory: A wholesaler has goods being transported from the manufacturer to their warehouse.
Cycle Inventory: A grocery store maintains a regular stock of perishable and non-perishable goods.
Anticipation Inventory: A toy manufacturer increases production in preparation for the holiday season.
Safety Stock: An online retailer holds additional inventory to avoid stockouts during peak sales periods.
Buffer Inventory: A pharmaceutical company maintains a surplus of critical medicines to meet unexpected demand or supply disruptions.
Obsolete Inventory: A technology company disposes of outdated smartphones that are no longer in demand.
Consignment Inventory: A bookstore displays books supplied by publishers on a consignment basis.
Excess Inventory: A retail store ordering more units of a seasonal product than the actual customer demand, leading to unsold items after the season.
Decoupling Inventory: It’s important to have a buffer stock of critical components in a manufacturing plant. This helps prevent disruptions in production, even if the supply chain faces delays.
Theoretical Inventory: To calculate how much raw material is needed for production, look at past demand and production efficiency. Do this without thinking about outside factors.
Understanding Inventory Turnover Ratio
Inventory turnover ratio is a key metric that measures how efficiently a company manages its inventory. It is calculated by dividing the cost of goods sold by the average inventory value during a specific period. A high inventory turnover ratio indicates that a company is effectively selling its inventory and minimizing holding costs. Conversely, a low ratio suggests inefficiency in inventory management and potential issues with overstocking or slow-moving products.
Importance of Inventory Control
Inventory control plays a vital role in optimizing the balance between supply and demand. Effective inventory control helps a company keep the right amount of inventory. This reduces costs and makes customers happier. It involves strategies such as forecasting demand, setting reorder points, implementing safety stock levels, and monitoring stock levels regularly.
By implementing inventory control measures, businesses can achieve several benefits, including:
Cost Reduction: Proper inventory control helps reduce holding costs, such as storage, insurance, and obsolescence expenses.
Improved Cash Flow: Optimized inventory levels prevent excessive investment in inventory, freeing up cash for other business needs.
Enhanced Customer Service: Adequate inventory control ensures products are readily available, leading to improved customer satisfaction and loyalty.
Reduced Stockouts: Efficient inventory control minimizes the risk of stockouts, ensuring that customers' demands are consistently met.
Importance of Inventory Management
Inventory management involves more than just controlling inventory. It takes a comprehensive approach to handling inventory at every stage of its lifecycle. It involves activities such as procurement, storage, tracking, and order fulfillment. Effective inventory management enables businesses to streamline operations, reduce costs, and maximize profitability.
Some key benefits of inventory management include:
Optimized Supply Chain: Good inventory management keeps goods flowing smoothly. It helps avoid disruptions and delays in the supply chain.
Accurate Demand Forecasting: Inventory management allows businesses to accurately forecast demand, enabling proactive planning and production scheduling.
Efficient Resource Allocation: By managing inventory effectively, businesses can allocate resources more efficiently, reducing waste and improving productivity.
Effective Order Fulfillment: Inventory management ensures timely order fulfillment, improving customer satisfaction and reducing order processing time.
What is Inventory Analysis?
Inventory analysis involves the evaluation of inventory data to gain insights into inventory performance, trends, and optimization opportunities. It helps businesses make informed decisions regarding inventory control, procurement, and demand forecasting. Inventory analysis typically includes metrics such as inventory turnover ratio, stockouts, carrying costs, and lead times.
Benefits of Inventory Analysis
Performing regular inventory analysis offers several benefits to businesses, including:
Identifying Slow-Moving or Obsolete Inventory: Inventory analysis helps identify items that are selling slowly or are no longer useful. This allows businesses to take actions like marking them down or disposing of them.
Optimizing Reorder Points: Businesses can look at inventory data and demand patterns. This helps them set the best reorder points, which reduces stockouts and excess inventory.
Improving Forecasting Accuracy: Inventory analysis gives useful information for predicting demand. This helps businesses make better forecasts and avoid having too much or too little stock.
Cost Reduction: Through inventory analysis, businesses can identify cost-saving opportunities such as reducing carrying costs, optimizing storage space, and negotiating better supplier terms.
Inventory Best Practices
Implementing effective inventory management practices can significantly improve operational efficiency and profitability. Here are some best practices to consider:
Regular Inventory Audits: Conduct regular physical inventory audits to ensure accuracy and identify any discrepancies.
Automated Inventory Tracking: Utilize inventory management software to automate tracking, streamline processes, and improve data accuracy.
Demand Forecasting: Implement robust demand forecasting methods to predict future demand accurately and optimize inventory levels.
ABC Analysis: Prioritize inventory based on its value and impact on the business using the ABC analysis method. Focus on managing high-value items more closely.
Collaboration with Suppliers: Build strong relationships with suppliers. This will help ensure timely deliveries, negotiate better terms, and access real-time inventory information.
Conclusion
Inventory management is a critical aspect of running a successful business. By understanding the various types of inventory, implementing effective inventory control measures, and utilizing inventory analysis, businesses can optimize their operations, reduce costs, and enhance customer satisfaction. By following Dynamic Distributors best practices, businesses can gain a competitive edge. They should also keep checking their inventory performance to stay ahead in today's market.
Related Blogs:
FAQ's Of Inventory
Q: What is the purpose of inventory management?
A: The goal of inventory management is to make sure a company has the right amount of inventory at the right time. This helps reduce costs and increase customer satisfaction.
Q: How often should inventory be counted?
A: The frequency of inventory counting depends on the business's size, complexity, and industry. Small businesses may count inventory annually, while larger businesses may count it more frequently, such as quarterly or monthly.
Q: What are the consequences of overstocking inventory?
A: Overstocking inventory can result in increased holding costs, such as storage expenses and the risk of obsolescence. It uses up money that could be invested in other areas. It might also cause shortages of other products because there isn’t enough storage space.
Q: What are the consequences of understocking inventory?
A: Understocking inventory can lead to stockouts and missed sales opportunities. It can also result in dissatisfied customers and damage to the business's reputation.. It can also result in rush orders, higher costs, and disruptions in the supply chain.
Comments