Optimizing Warehouse Layout for Overstock and High Turnover Products
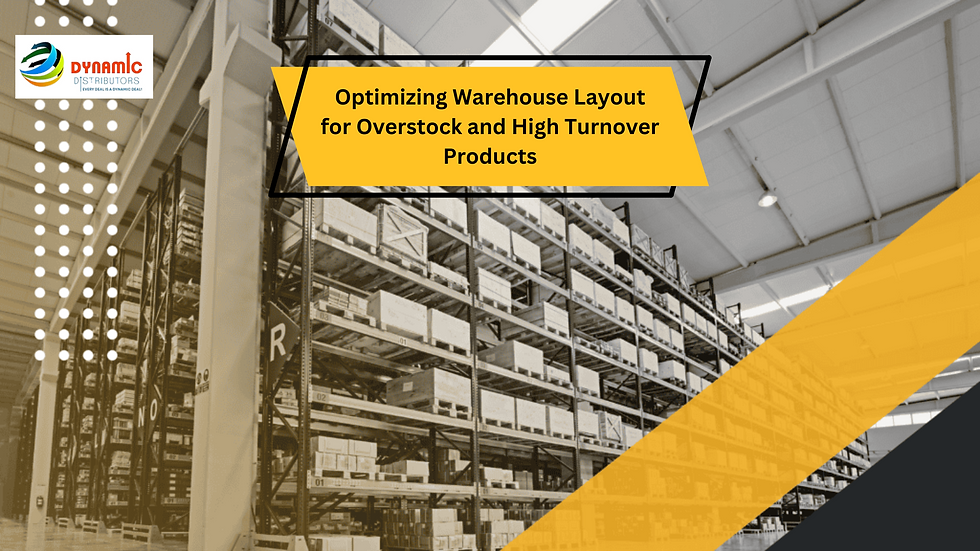
A warehouse layout is crucial for managing inventory effectively. Overstock products and high-turnover items require different handling strategies. Overstock takes up valuable space and can lead to inefficiencies if not stored properly. On the other hand, high-turnover products need quick access to maintain a smooth order fulfillment process. A well-optimized layout ensures efficiency, reduces operational costs, and improves productivity.
This article will explore the best practices for designing a warehouse layout that efficiently manages overstock and high-turnover products.
Overstock and High-Turnover Products
Overstock Products
Overstock refers to inventory that exceeds demand. It happens due to inaccurate demand forecasting, supplier delays, bulk purchasing discounts, or seasonal shifts. While some overstock is intentional, excessive overstock can lead to higher storage costs, product obsolescence, and wasted warehouse space.
Overstock products should be stored strategically. They should not block operational areas or interfere with the movement of frequently needed items. Instead, they should be stored in separate, less accessible zones, allowing for organized retrieval when required.
High-Turnover Products
High-turnover products are items that sell quickly and require frequent restocking. These products must be stored in easily accessible locations to minimize the time taken for picking and packing.
A poor layout can slow retrieval times, increase worker fatigue, and delay order fulfillment. Placing high-turnover products near picking and shipping areas can significantly improve warehouse efficiency.
Related Blog:
Key Warehouse Layout Strategies
1. Maximizing Space Utilization
Space is one of the most valuable assets in a warehouse. Overstock should be stored efficiently without wasting space, while high-turnover products need to be easily accessible.
Vertical storage, compact shelving, and designated overstock zones help optimize available space. High-turnover items should be placed at eye level or in easy-to-reach areas to speed up picking times.
2. Reducing Worker Travel Time
The more time workers spend walking through the warehouse, the less efficient the operations. High-turnover products should be stored near the shipping and receiving areas, reducing travel time. Overstock, which is retrieved less frequently, can be stored in the regions that do not interfere with daily operations.
Using conveyor systems or automated picking solutions can reduce the time spent moving products.
Related Blog:
3. Aisle and Pathway Design
Aisles must be wide enough to move forklifts, pallet jacks, and workers safely. High-traffic areas should have wider aisles for smooth operations, while overstock storage can have narrower aisles since it does not require constant access.
A one-way aisle system can improve workflow by preventing congestion and organizing movement.
Zoning for Overstock and High-Turnover Items
1. Fast-Moving Product Zones
These zones should be located near shipping and receiving areas.
Flow racks and dynamic shelving can be used to improve accessibility.
Easy restocking helps prevent delays in order fulfillment.
2. Overstock Storage Areas
Overstock should be kept in bulk storage zones separate from the main picking areas.
High racks, mezzanines, or deep shelving can be used to save space.
FIFO (First-In-First-Out) and FEFO (First-Expired-First-Out) methods should be applied to ensure proper inventory rotation.
3. Seasonal Overstock Storage
Some overstock is temporary, such as holiday-related inventory.
Modular shelving systems allow for flexible storage.
Overflow warehouses or offsite storage can be used when necessary.
Picking and Storage Optimization
1. Product Slotting Optimization
Slotting involves placing products in the most efficient locations based on demand, size, and handling requirements. High-turnover items should be placed in prime picking locations, while overstock should be stored in less active zones.
Dynamic slotting can improve warehouse efficiency, where product locations change based on demand fluctuations.
2. Cross-Docking for High-Turnover Items
Cross-docking is a process where incoming products are directly transferred to outgoing shipments without being stored in the warehouse. This reduces handling time and storage requirements, making it ideal for high-turnover items.
Implementing cross-docking minimizes storage costs and speeds up order processing.
3. Automation in Storage and Retrieval
Automated solutions can significantly improve efficiency in managing overstock and high-turnover products:
Conveyor belts reduce manual handling for high-turnover items.
Barcode and RFID tracking systems improve inventory accuracy.
Automated storage and retrieval systems (AS/RS) reduce picking time and optimize space usage.
Related Blog:
Using Technology for Better Layout Management
1. Warehouse Management Systems (WMS)
A Warehouse Management System (WMS) tracks inventory in real time, helps assign optimal storage locations, and improves order accuracy.
With a WMS, managers can identify slow-moving and fast-moving products, making it easier to reorganize the warehouse as demand changes.
2. IoT and Smart Sensors
Smart sensors can track product movement, monitor stock levels, and even detect environmental conditions such as temperature and humidity. These sensors help prevent overstock buildup and optimize product placement.
3. Data Analytics for Continuous Improvement
Data analytics plays a vital role in improving warehouse efficiency. By analyzing product movement patterns, managers can:
Identify inefficiencies in the layout.
Adjust storage zones based on demand fluctuations.
Improve order fulfillment speed.
A data-driven approach allows warehouses to remain flexible and responsive to market trends.
Best Practices for Optimizing Warehouse Layout
1. Implementing an ABC Analysis
ABC analysis classifies inventory based on turnover rates:
A-items: High-turnover products must be stored in the most accessible locations.
B-items: Moderate turnover items stored slightly further away.
C-items: Slow-moving or overstock items stored in less accessible areas.
This system ensures high-demand products are always within reach, while overstock is stored efficiently without interfering with operations.
Related Blog:
2. Balancing Aisle Width and Storage Density
A balance between aisle width and storage density is crucial. Narrow aisles save space but can slow down movement. Wide aisles improve accessibility but reduce storage capacity.
The ideal design considers workflow efficiency, storage needs, and equipment movement.
Related Blog:
3. Regularly Reviewing and Adjusting the Layout
A warehouse layout should not be static. Regular reviews help identify inefficiencies and allow continuous improvements based on changing demand and operational requirements.
Conclusion
Optimizing a warehouse layout for overstock and high-turnover products improves efficiency, reduces costs, and enhances productivity. Overstock should be stored strategically to avoid interfering with daily operations, and high-turnover products must be placed in accessible locations to speed up order fulfillment.
Zoning strategies, slotting optimization, and automation ensure that both types of inventory are managed efficiently. Technology, such as WMS and data analytics, helps monitor inventory movement and adjust when necessary.
A well-structured warehouse layout is not a one-time setup but a continuous improvement process. By regularly analyzing product demand and warehouse efficiency, businesses can maintain smooth operations and reduce unnecessary costs.
By following these best practices, warehouses can achieve a balance between effective overstock storage and seamless high-turnover product management, leading to better overall performance.
コメント